Partner in Pet Food
Z papíru do digitální éry: Příběh úspěchu předního výrobce krmiva pro domácí mazlíčky
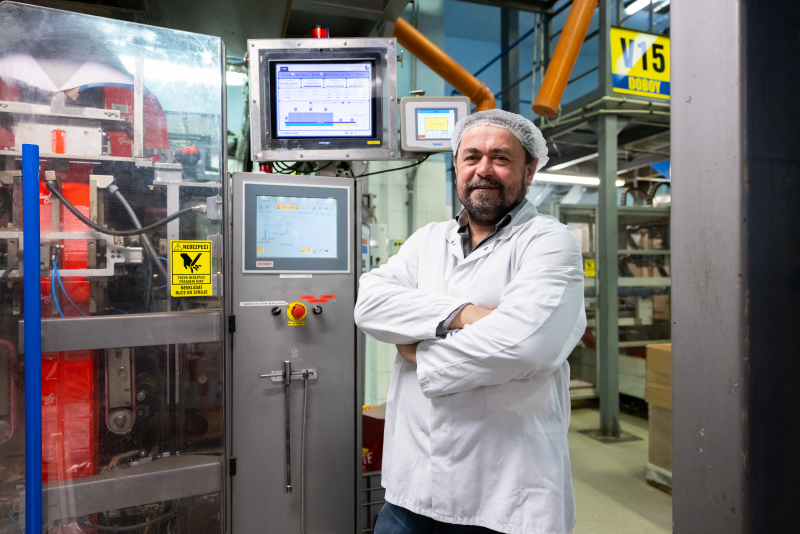
MES SoftLi už k zefektivnění výroby úspěšně využívá mnoho významných společností nejrůznějších zaměření. Jednou z nich je Partner in Pet Food – přední výrobce krmiv pro domácí mazlíčky, který působí v 10 evropských zemích. Jeho firemní kulturu charakterizuje hlavně výkonnost a schopnost najít řešení v každé situaci. Tedy stejné vlastnosti, jaké má náš MES. Proto není překvapení, že vzájemná spolupráce funguje skvěle. Na podrobnosti jsme se zeptali production managera PPF, pana Zdeňka Zahejského.
Kdy jste začal přemýšlet o digitalizaci výroby?
Asi hned po mém nástupu do PPF před 6 lety, kdy veškeré záznamy o výrobě byly ještě vedeny v papírové podobě. A v některých oblastech se dokonce nevedly vůbec. To byl velký rozdíl oproti mému předchozímu působišti, kde jsme pro výrobu na vstřikolisech systémy monitoringů využívali.
Můžete porovnat tehdejší situací s tou dnešní?
Myslím, že díky tomu, co zde máme implementováno, jsme dnes mnohem dál než drtivá většina firem.
Jak probíhala vaše digitalizace výroby?
Nejprve jsme implementovali MES SoftLi jako takový. Je to systém sběru dat, na jehož základě můžeme vyhodnocovat data a dělat analýzy či reporty. Jak pro nás, tak pro vedení a majitele společnosti.
Brzy po vyzkoušení MESu jsme zjistili, že je užitečný, že nám vyhovuje a že management je spokojený. Proto jsme se rozhodli ho dále rozvíjet a postupně implementovali další a další moduly, až se nám podařilo vybudovat poměrně robustní systém, který dnes nemá v rámci skupiny PPF obdoby. Kolegové z jiných továren k nám často jezdí pro inspiraci – a já jim vyprávím, jak jsme díky takto komplexnímu MESu výrazně zefektivnili výrobu.
Co kolegy ze zahraničí nejvíce zaujme?
To zpravidla záleží na profesi, protože vedoucího výroby zajímají jiné moduly než kvalitáře. Na všechny, včetně členů nejvyššího vedení, ale spolehlivě udělá velký dojem, když jim ukážu, že jsem vždy online, celou dobu vidím v reálném času obrazovku operátora a kdykoliv mu můžu ukázat aktuální reporting.
Vaše firma si zakládá na maximální flexibilitě v každé oblasti tak, aby byla co nejefektivnější. Přizpůsobili jste si tedy i MES na míru?
Ano, ve spolupráci se SoftLi jsme v systému modifikovali některé věci, aby MES zcela vyhovoval i našim hodně specifickým potřebám. Plně jsme ho integrovali a propojili s naším ERP systémem. Dnes oba systémy fungují v naprosté symbióze a automaticky si mezi sebou vyměňují potřebná data.
Můžete uvést nějaký příklad takové komunikace mezi systémy?
Z MESu například zapisujeme data přímo do ERP, zatímco z ERP si bereme údaje z kusovníků. Je toho opravdu hodně, protože jak už jsem říkal – ten systém je dnes opravdu robustní a vyladěný do nejmenších detailů. A právě to nám poskytuje značnou výhodu před konkurencí.
Vy máte zavedený i systém pro plánování, že?
Ano. Nechali jsme si ho až úplně na konec. Zpětně to už asi můžu přiznat, ale já se opravdu bál, že to nevyjde a on nebude fungovat.
Proč?
V mém bývalém působišti to tak totiž bylo. Dvakrát jsme se o něj pokoušeli – a dvakrát jsme od toho upustili, protože to bylo příliš komplikované pro plánaře i výrobáky. Bylo to pro ně hodně nepřehledné a oni pak stále upřednostňovali práci v Excelu. Vždycky jsme se nakonec zase vrátili k Excelu, protože byl jednodušší.
V čem to bylo u PPF jiné?
Systém výroby byl podobný. Také se plánovalo v ERP v kombinaci s Excelem a neexistoval žádný Gantt chart nebo vizualizace. Zásadní rozdíl byl ale s dodavatelem MESu a v jeho implementaci.
Se SoftLi jsme si hned ze začátku vzájemně vyjasnili možnosti a očekávání. Specifikovali jsme, co od systému chceme a oni ho pak upravili podle našich potřeb. Tento proces samozřejmě prochází určitým vývojem a chvíli trvalo, než jsme ho stoprocentně vyladili, ale dneska už šlape na jedničku. Mám z toho velkou radost, protože pro mě jde o první instalaci planneru, která v praxi opravdu funguje a kterou rádi používají i všichni zaměstnanci.
Jako manažer vždy chci předcházet situacím, kdy nadřízený něco tlačí, ale podřízení to nepoužívají, protože to místo usnadnění práce berou jako zátěž a snaží se najít nějakou výhybku.
Já ale každý den vidím, jak lidi s MES SoftLi pracují. Na ranní poradě se promítají life data z minulého dne, která ihned analyzujeme. Plánaři zase moc rádi využívají planner, který jim ulehčuje život. Ta pozitivní změna se promítá i do dalších oddělení, kde si například jednoduše sledují, kdy se která zakázka pojede.
Z pozice manažera mě těší sledovat to, že tady je MES „živý“ a že ho zaměstnanci vzali za svůj. Vnímají, že ho k práci potřebují a že dnes jde o podstatě o nutnost.
Excel už tedy vůbec nevyužíváte?
Excel již používáme pouze na určité výstupy. Ale to je tím, že operátoři ve výrobě byli dlouhé roky zvyklí na excelový systém předávání plánu výroby, a proto jsem do toho zatím ještě nesahal. Rozhodl jsem se totiž pro implementaci mírnější cestou. Jdu krok po kroku a postupně přesvědčuji lidi o potřebě se posunout dál.
Každá další implementace je jednodušší a jednodušší, protože zaměstnanci chápou smysl toho, proč to děláme. A že jim ta změna ulehčí práci. Jen to musí ještě přirozeně proniknout až na úroveň posledního operátora, než přejdeme na kompletní digitalizaci.
Spolupracujete se SoftLi i v rámci tohoto mezikroku?
Ano, vymysleli jsme takový mezistupeň, během něhož se tento zažitý excelovský sheet vygeneruje přímo z planneru. Plánař to tedy nemusí manuálně přeťukávat. Další fází už bude úplné vyřazení Excelu z našeho workflow. Operátoři, kteří mají přístup k webovým klientům, budou mít náhled přímo do planneru a budou se moci podívat přímo na to, co jede.
Vyskytly se během implementace MES SoftLi nějaké problémy?
Jedna komplikace tu je, ale to není chyba MESu. PPF má standard prezentací, který každá pobočka musí dodržovat . My se jím neřídíme, protože už nepíšeme fixami na whiteboardy či papír, ale snažíme se vše dostat do obrazovek. Všude používáme televize a life data. A jsme za to penalizováni.
V korporátech zkrátka občas trvá, než si vrcholní manažeři na podobné inovace zvyknou. I proto leckdy sveřepě trvají na „starých dobrých“ metodách z minulého století, ačkoliv děláte přesně to, po čem už tehdy japonští specialisté na lean production nebo průkopníci průmyslu 4.0 volali, ale ještě to nebylo technologicky možné.
Jenže tohle jde ještě mnohem dál. Jsme mnohem dále, než je standard. Ale v tabulce pro to nemají další políčko v hodnocení. Na škále od 1 do 5 bychom měli dostat 6, jenže ta kolonka tam není. Proto máme sražené hodnocení, jelikož vlastně nedodržujeme standard korporace.
Čeho jste se nejvíc obával, když jste se rozhodli, že zavedete MES?
Já jsem se s PPF v té době seznamoval a nevěděl jsem, jaké tu jsou možnosti. Snaha o zavedení něčeho nového brzy po nástupu do nové firmy s sebou vždy přináší určité obavy. Navíc musíte přesvědčit nadřízené o tom, že danou věc má smysl implementovat.
Pak tu jsou samozřejmě obavy i na straně implementátorů. A pokud ta firma stále jede v Excelu a nemá nic zavedeného, tak je dost složité jim říci: „Hele, já potřebuju tolik na tohle tolik, nebo tolik na toto. Anebo tolik na tohle. Záleží na tom, jak daleko chceme v rámci implementaci dojít.“
PPF bylo v době mého příchodu z pohledu MESu pole neorané. Nevěděl jsem, jak daleko můžeme zajít, a jestli vůbec moje snaha vyústí v nějakou implementaci. Toho jsem se fakt bál, protože firma tehdy potřebovala i jiné věci – investici do strojů, pravidelné údržby atd.
Co tedy rozhodlo o tom, že vaše myšlenka dostala zelenou?
Můj šéf jde s dobou a je osvícený, takže když jsem mu ukázat principy MESu od Softli a všechno jsem mu vysvětlil, ihned se do toho ponořil. Zajímal se, něco si přečetl, popovídal si se známými a rozhodl se do toho jít. Domluvili jsme se, že uděláme první nasazení.
Jak to probíhalo?
První implementace byly zkušební. Nebyly proto moc drahé, ale daly nám šanci přesvědčit přímé nadřízené a ukázat jim přínos systému. To se povedlo, takže jsme postupně rozšířili MES na další, pro nás důležité, procesy.
Každý rok jsme postupně přidávali další modul, někdy i dva. A později se zavedly některé moduly i mimo rozpočet, když se ukázalo, že nám MES pomůže vyřešit nějaký aktuální problém – a nadřízení nám schválili mimořádnou investici. Až tak příjemně byli překvapení tím, co vše lze s MES jde dělat.
Dnes už je firma parádně zasíťovaná, takže si můžeme vychutnávat všech výhod, které systém nabízí a investovat do dalších projektů.
Zmínil jste, že vrcholný management přesvědčily první rychlé přínosy v rámci zkušební implementace. O co šlo?
Pro mě osobně bylo velkým pozitivem to, že jsem viděl life data posbíraná z výroby a dokázal tak okamžitě analyzovat problémy, které tam byly.
Já jsem do PPF přišel z jiného typu výroby a odlišného prostředí, a tak jsem nejprve potřeboval detailně pochopit, jak to tu vlastně funguje. Třeba na ranních poradách jsme řešili, co se dělo za předchozí den a já se moc nechytal.
Pak jsem ale viděl life data a zjistil, že ve výrobě byla hromadu krátkých prostojů, které se nikde nezaznamenávaly. Stroj třeba fungoval 2 minuty a pak minutu stál, poté 3 minuty vyráběl a dalších 30 vteřin dál.
To v souhrnu za 24 hodin výroby už znamenalo opravdu velké prostoje, které ale operátoři v ručně psaných záznamech neuvedli. Až díky reálným datům jsem mohl říct: „Tady je nějaký problém a musíme se zaměřit na tohle a tohle.“
S podobnými analýzami v ruce jsem tedy mohl ukázat nadřízeným: „Hele, tenhle stroj vykazuje největší poruchovost. Pojďte do toho investovat a opravme to.“
Díky tvrdým datům jsme mohli přesně odhalit, co je rozbité, nefunkční či na hraně životnosti, – a pak efektivně investovat do opravy či náhrady stroje. Víme tedy, jaké problémy průběžně přicházejí i jak je máme správně řešit. A naše výkonnost a efektivita tak i nadále stoupá.
Dá se nějak vyčíslit, kolik jste zavedením MES ušetřili? A jak se zvedla efektivita a snížily prostoje?
V našem typu výroby se toto jen těžko přesně vyčísluje. Jsme totiž velmi orientovaní na zákazníka a jeho potřeby, a proto se nám v závislosti na jeho požadavcích průběžně mění portfolio produktů. Každý kvartál obměníme až 20 % portfolia. A každý výrobek přináší trochu jiné a specifické problémy…
Proto nelze jednoznačně říct, že máme například o 10 % zlepšenou výkonnost v OEE parametru, protože s nájezdem nových produktů se objevují nové těžkosti, což metriku OEE rázem trochu zkresluje.
Obecně ale mohu potvrdit, že za těch 5-6 let jsme produktivitu zvedli o cca 20 %.
Zmínil jste, že máte zkušenost s implementaci MES už z minulé práce. Můžete ty dva procesy porovnat?
V minulé firmě jsem MES implementoval s velkou nadnárodní společností, zatímco v PPF jsme zvolili menšího dodavatele. A musím říct, že se mi mnohem lépe pracuje s tím menším. Velká firma nedokáže sáhnout do svých procesů a nedokáže efektivně udělat nějakou úpravu, kterou by modifikovala systém podle potřeb zákazníka.
Se SoftLi se vždy domluvím na přizpůsobení dle mých požadavků, byť se stále pohybujeme v rámci nějakého standardu. Jejich flexibilita je oproti velkým dodavatelům úplně jinde a já díky tomu nemusím řešit problémy, které mají naše sesterské závody s jinými dodavateli.
Podpora ze strany SoftLi je maximální. Když potřebuji pomoc, tak zavoláme a okamžitě dostanu odpověď.
Jaký další modul plánujete do budoucna?
Za mě je to kvalitářský modul – dokumentace k výrobku, modul checklistů a formulářů. Těším se, až díky podrobné evidenci a výrobním podkladům na bázi záznamu teplot, údajích o vlhkostech a dalších datech ještě zefektivníme naši výrobu.
Děkujeme za rozhovor.
Chcete také zefektivnit výrobu?
Pomáháme malým i velkým výrobním firmám být až o 20 % efektivnější. Bez papírů. Bez prostojů. Bez výmluv.
Jako jediní nabízíme bezplatné a okamžitě dostupné DEMO i možnost nezávazného otestování systému přímo na vlastních strojích.